Kansanshi Mining, a First Quantum-owned company located in Zambia, is leveraging Accelovant’s fibre-optic sensors to solve its arcing and electronics failure and signaling issues at the major copper mine.
Kansanshi operates one of the world’s largest and most productive copper mining and smelting sites. The smelting operations use wet electrostatic precipitators (ESP) to clean sulphur dioxide gas by removing acid mist (aerosols) and dust particles that can result in a toxic concentrated sulphuric acid effluent. While ESPs are considered one of the most effective process scrubbers in this application, process temperature control has long been an impediment to more extensive use. Control of the ESP requires temperature measurement technology that can withstand simultaneously high voltage, high temperature range, and high electromagnetic fields.
In application, the wet ESP utilises high-voltage electromagnetic fields to attract or impel different molecules in a gas stream to affect separation and collection. It has one field consisting of discharge electrodes in the centre of tubular collecting electrodes. The gas is ionised by the corona discharge of the discharge electrodes. The particles contained in the gas are charged and migrate under the influence of the electrostatic field to the grounded electrodes.
In the case of the Kansanshi copper smelter, the sulphur dioxide gas from the smelter is moved through the wet ESP plants to separate the acid mist and dust from the gas stream. The acid mist is highly corrosive and, if not removed from the gas, it is capable of damaging downstream equipment such as gas blowers and ductwork.
To operate correctly and prevent damage to the electrical and ceramic components of the wet ESP, it must be heated to a consistent temperature between 325-340°C. Operating in this range will prevent condensation of the mist. If condensation occurs, it substantially increases the risk of short circuiting that can lead to poor unit performance.
Historically the ESPs employed conventional in-stream thermocouples and/or Resistance Temperature Detectors (RTD), both highly susceptible to electrical noise. When employed, these sensors were unreliable and represented a flashover risk due to the high voltage environment.
Pieter Oosthuizen, Control Instrumentation Superintendent, and Bodrick Mumba, Superintendent Operations Sulphuric Acid Plant, both work to maintain consistent and reliable operation of the smelting plant and ESPs. The ESPs operate around the clock in paired sets, processing a constant stream of smelter gas.
According to Mumba, if one ESP is operating outside of the proper temperature range, the volume of smelter gas has to be reduced by cutting down concentrate treatment in the primary smelting furnace until the unit is returned to proper operating status.
“If the temperature drops below the setpoint there is great risk of acid misting and condensing on the ceramic insulators in the ESP,” Mumba said. “If the ceramics are damaged, potential downtime to repair would certainly reduce throughput and output of the plant.”
Maintaining proper temperature control in an extremely harsh environment
In a harsh operating environment surrounding the wet ESPs (high voltage, electrical noise and high temperature), monitoring and managing precise temperature levels through the use of in-stream sensors was a difficult and highly unpredictable exercise. The ESP units supplied by Metso Outotec are designed to allow the use of multiple different sensors that conform to a standardised form factor, enabling the operator to install the most effective sensor for the use case.
“The ESP units operate with a typical 45 kV charge atcurrents in the 500-600 milliamp range,” Oosthuizen said. “In this kind of environment, there is tremendous electromagnetic noise and induced currents in anything that is conductive or that utilises electronics. This includes the thermocouples and RTDs that are typically employed to monitor high temperatures in industrial settings. We tried many different device types, but in all cases the electronics would burn out and fail due to the stray electromagnetic fields.”
Oosthuizen noted that in the smelting plant environment, both RTD and thermocouple devices were subject to high-voltage flashovers which can damage them, or, at a minimum, disrupt the transmitted electrical signals from the sensor to its controller. Such plant conditions contribute to high sensor failure rates, and difficulty in maintaining signals essentially prevented automated control.
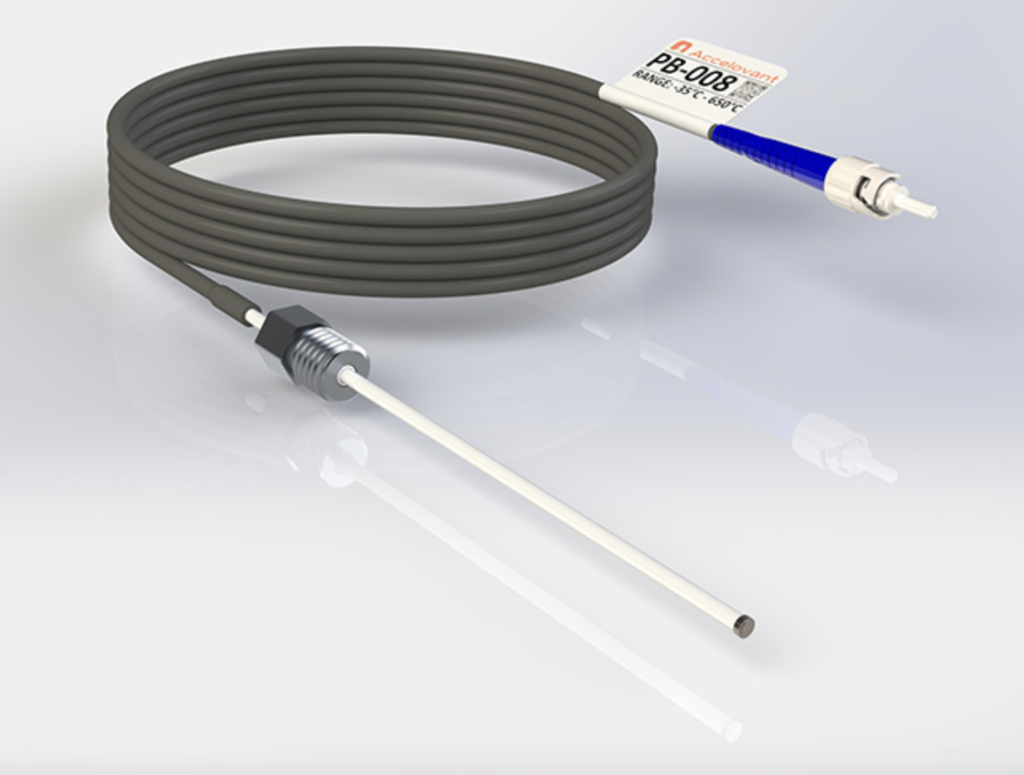
Operating under manual control was more costly, and meant operators had to make regular temperature readings and adjust operational parameters to maintain the proper range. In a complex operating environment with many variables, making these adjustments manually was an ongoing process that consumed substantial personnel time and cost.
The high failure rate of sensors and inability to utilise automated controls were limiting factors in maintaining the reliable and consistent operation of the ESPs and of the productivity of the entire plant. In their search for a workable solution, Mumba and Oosthuizen learned that fibre-optic temperature sensors were widely employed in harsh environments due to their immunity to electrical noise.
“As we researched fibre-optic sensors, it became clear that the inherent immunity to electrical noise could solve our arcing and electronics failure and signaling issues, but we also needed to address the high-temperature operating conditions,” Oosthuizen said. “While operating specifications for most fiber-optic sensor suppliers on the market did extend up to the 325-340° C range, our requirements were toward the top end of the recommended range, so we were a bit apprehensive about product in-service longevity. That’s when we discovered a Canadian supplier that specialised in high temperature fibre-optic sensors.”
The team found a new class of fibre-optic sensors from Canadian manufacturer Accelovant that seemed to address both of the key issues they were trying to solve.
A new class of fibre-optic sensors
Fibre-optic sensors use only the energy of light to measure temperature. Because they contain no electrical function, they are immune to the adverse electromagnetic affects inherent in conventional sensors such as thermocouples and RTDs. While currently employed widely in industrial applications, they are generally limited to 250˚C. Above that temperature, the organophosphorus compounds used to generate the temperature measurement optical signal will begin to fail.
“Accelovant specialises in high temperature fiber optic sensors,” Michael Goldstein, CEO for Accelovant, said. “We went back to the basics of material science and invented a patented ceramic-like optical material to create a new class of fibre-optic temperature sensors that could withstand much higher temperatures and offer longer service life at temperatures exceeding 450°C.”
In April 2022, Accelovant fibre-optic sensors were installed in one of the matched pairs of ESPs operating in the plant. Shortly after installation, Oosthuizen was ready to experiment with utilising the automated controls available in the plant management software.
“We knew that, in theory, the fibre-optic sensors would outperform the electronic sensors, but wanted to be certain that it was also the case in practice,” he said. “After several months of observation and testing, we converted to operating the temperature controls on those two ESP to automatic – for the first time in more than eight years of operation.“
Accelovant fibre-optic sensors delivered the high-temperature longevity and electromagnetic immunity necessary to provide reliable and consistent temperature monitoring and control within the wet ESP copper smelting operations at Kansanshi, the company said.
Oosthuizen reports that after 11 months in service, the Accelovant fibre-optic sensors were performing as demanded and enabled full automated control of the ESPs. “In the years that the ESPs have been in operation, we have never been able to operate without a sensor failing for such a lengthy period,” he noted.
The stability of the Accelovant sensors has finally allowed for automated management of stream temperatures and eliminated some of the operational challenges at the plant.
Mumba added: “The Accelovant sensors have increased our efficiencies by eliminating manual temperature adjustment – a process that could take multiple iterations to achieve the desired results. They provide reliability that allows us to concentrate our time on other matters.”